What you can do with IO-Link
In a factory, there are thousands of sensors and actuators operating on production lines and equipment, and IO-Link makes it possible to monitor and setup information from many sensors and actuators that could not be centrally managed in the past, at the controller-level.
The data that can be handled by IO-Link communication is shown on the left for a sensor.
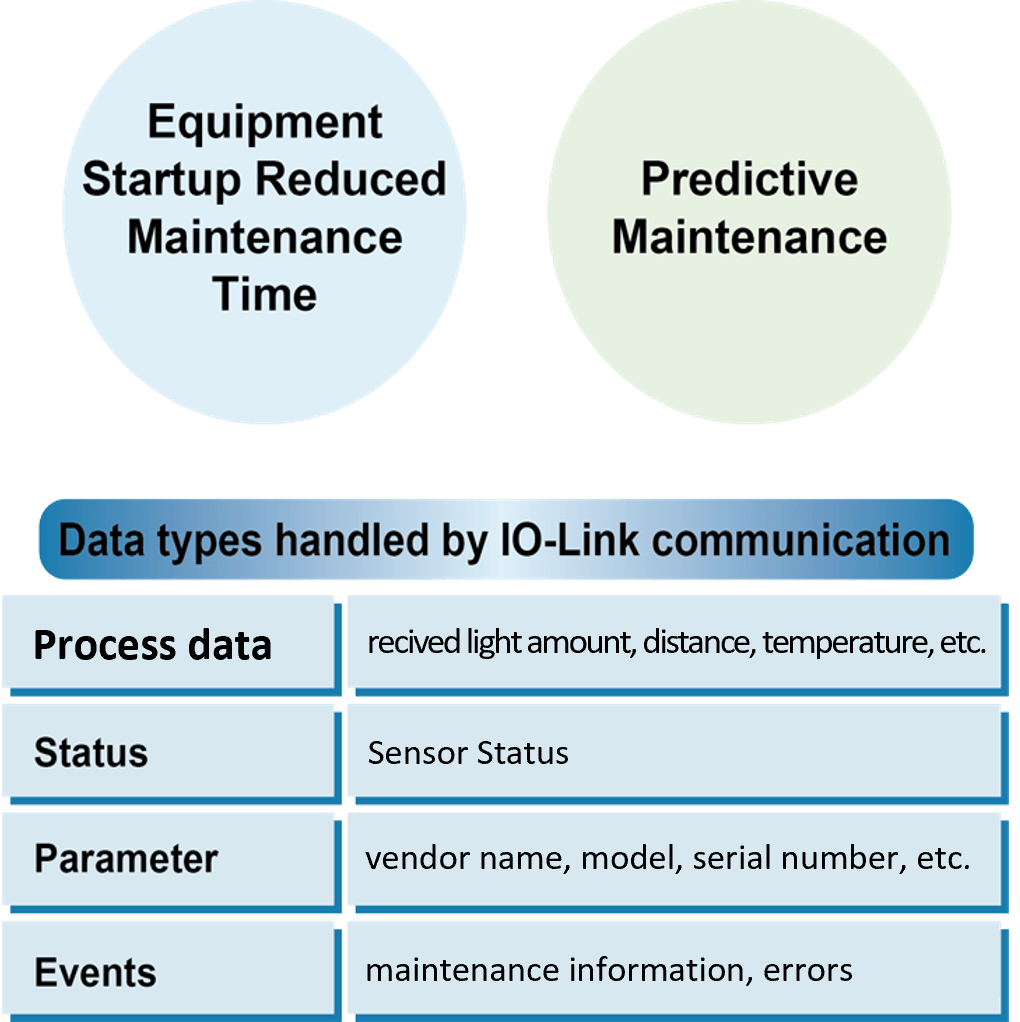
When changing lots or types, batch sensor settings and I/O checks can be performed from the PLC, and set-up information can be imported from IO-Link Master when replacing sensors. As a result, equipment start-up and maintenance time can be reduced.
In recent years, there has been an increasing need for "preventive maintenance" to detect signs of equipment failure. Many IO-Link devices are pre-installed with these functions, making it possible to easily create "preventive maintenance" systems.
POINT
IO-Link reduces equipment start-up and maintenance time.
This means that batch sensor settings and I/O checks can be performed from PLC. In addition, an automatic restore function allows the same settings as those of the sensor before replacement to be imported from the IO-Link Master, so maintenance can be completed simply by wiring.
Number and type of IO-Link compatible devices
There are 16 million IO-Link compatible devices as of the end of 2019.
The number of nodes has approximately doubled in two years from 8.1 million at the end of 2017.
There is a wide range of IO-Link compatible devices.
Example: photoelectric sensors, displacement sensors, switches, RFID, actuators (driving devices), buzzers, indicator lights, etc.
IO-Link Complete Guide
Back to top