- Selected Examples of
Laser Sensor-Based
On-Site Improvements
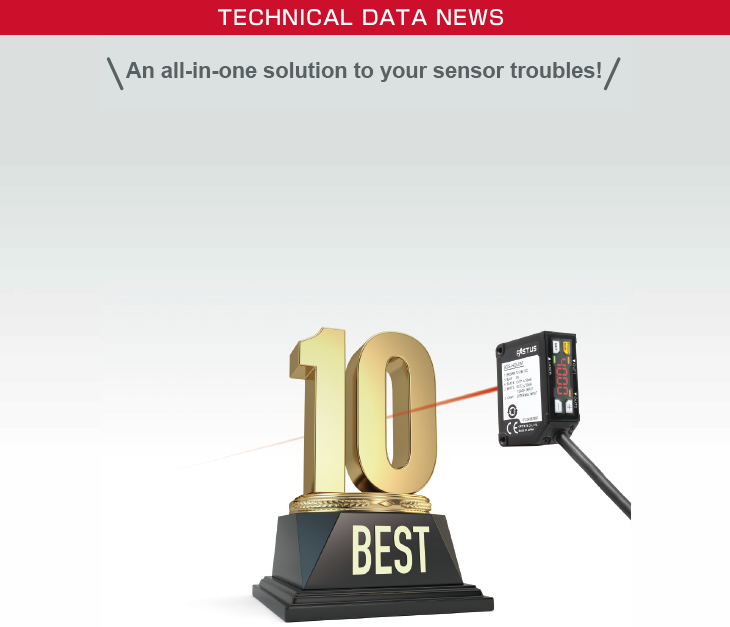
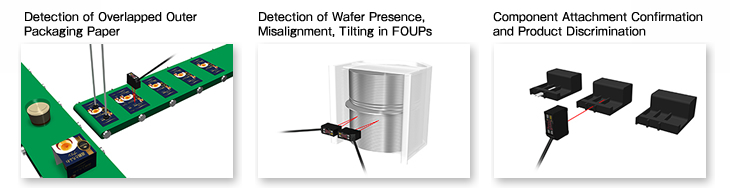
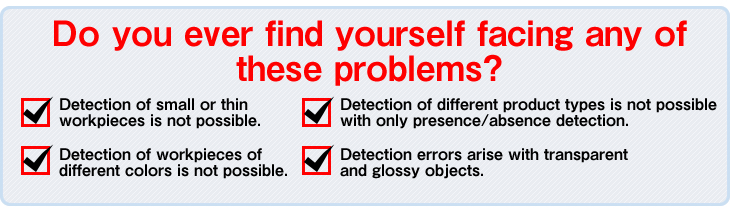
- Eliminate such problems with high-performance,
high-accuracy laser sensors!
Browse industry-specific process improvement examples! - Learn more about various process improvements made possible with high-performance, high-accuracy laser sensors being put to use in a wide variety of industries. Each application example details how detection is enabled even for workpieces that could not be detected using photoelectric sensors, and how using two outputs enable defect detection. The comprehensive descriptions of how to use just one sensor to improve applications that conventionally required two sensors also make this collection recommended reading for beginners.
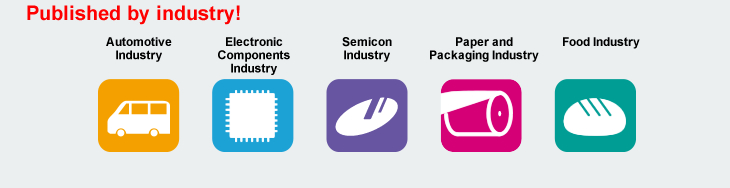
- Automotive Industry
-
- Automotive Component Positioning
- The BGS-HDL series is useful for positioning during automotive component assembly.
Detecting holes at an angle is difficult with a photoelectric sensor, but the BGS-HDL series includes an automatic mode that utilizes an optimal sampling period to ensure stable detection even when installed diagonally.
- Notable Points
• AUTO sampling period mode for improved detection when tilted
• Minimum detectable height difference of 0.8 mm even at a distance of 250 mm (BGS-HDL25T2)
-
- Shaft Direction and Motor Float Detection
- Using the BGS-HDL series makes it possible to determine the direction of an actuator shaft and to detect floating (flange detection) when a motor is attached.
With two control outputs, the BGS-HDL series is capable of separate detections by using Output 1 for determining the shaft direction, and using Output 2 for motor float.
This means that all the work in applications that would conventionally require two sensors can be done with just a single sensor. - Notable Points
• Two individual control outputs
• Minimum detectable height difference of 0.8 mm even at a distance of 250 mm (BGS-HDL25T2)
- Electronic Component Industry
-
- Parts Feeder Component Level Control
- The BGS-HDL series is ideal for controlling the height level of components in the parts feeder.
The BGS-HDL’s two control outputs can be used to ensure upper and lower limits by turning on Output 1 as a supply start signal when the remaining component quantity is reduced, and by turning on Output 2 as a stop signal when the component level increases sufficiently after supply start.
This means that all the work in applications that would conventionally require two sensors can be done with just a single sensor. - Notable Points
• Minimum detectable height difference of 0.8 mm even at a distance of 250 mm (BGS-HDL25T2)
• Two individual control outputs
• AUTO sampling period mode for improved resistance to colors and gloss
- Parts Feeder Component Level Control
-
- Component Attachment Confirmation and Product Discrimination
- The BGS-HDL series is used for confirmation of terminals attached to breaker components and for determining product type.
The two control outputs of the BGS-HDL series are used to check for the presence of the terminal (Output 1) and to detect different product varieties (Output 2).
This eliminates the need to use two separate sensors and ensures both processes are performed using a single device. - Notable Points
• Two individual control outputs
• Pinpoint terminal detection thanks to fine spot laser
- Semiconductor Industry
-
- Silicon Wafer Misalignment Detection
- The BGS-HDL series enables detection of silicon wafer misalignment on a wafer stage.
Misaligned wafers can be up to 5 mm higher than normal, while the BGS-HDL series is capable of detecting height differences of 0.08 mm, ensuring high-accuracy performance.
- Notable Points
• Minimum detectable height difference of 0.08 mm (BGS-HDL05T)
• AUTO sampling period mode for improved detection when tilted
- Silicon Wafer Misalignment Detection
-
- Detection of Wafer Presence, Misalignment, Tilting in FOUPs
- Two BGS-HDL series devices can be used to detect the presence, misalignment, and tilting of wafers in FOUPs.
The two control outputs of the BGS-HDL series are used to detect wafer presence (Output 1) and wafer misalignment (Output 2).
Wafer tilting is detected by the Output 1 ON/OFF timing of the right and left sensors.
- Notable Points
• Two individual control outputs
• Minimum detectable height difference of 0.8 mm even at a distance of 250 mm (BGS-HDL25T2)
Paper and Packaging Industry
-
- Cutter Positioning with Printing Machines (Thin Paper Detection)
- The BGS-HDL series is useful for positioning of cutters in printing machines.
Detection is performed when the paper hits against the stopper, and the cutter blade cuts the paper to the preferred size.
The BGS-HDL series’ ability to detect thicknesses of just 0.08 mm ensures high-accuracy detection even with paper thicknesses up to 0.5 mm.
In addition, stable detection is possible even for thin glossy paper even against a glossy background such as metal. - Notable Points
• Minimum detectable height difference of 0.08 mm (BGS-HDL05T)
• AUTO sampling period mode for improved resistance to colors and gloss
- Cutter Positioning with Printing Machines (Thin Paper Detection)
-
- Detection of Remaining Paper on Rolls
- The BGS-HDL series makes it possible to detect the amount of paper remaining on a roll.
Whereas conventional setups required regular monitoring by workers, the BGS-HDL series is able to turn Output 1 off when the paper material has decreased to a specified amount.
The ability to predict replacement timing in advance allows for a reduction in the time required for monitoring.
- Notable Points
• Small ø1 mm spot even at a distance of 250 mm (BGS-HDL25T2)
• Long-range detection (BGS-HDL25T2)
- Detection of Remaining Paper on Rolls
- Food Industry
-
- Detection of Overlapped Outer Packaging Paper
- The BGS-HDL series can be used to detect the presence of colorful outer packaging paper and whether the papers are overlapped.
The BGS-HDL series’ two control outputs enable simultaneous detection of both the presence of the outer packaging paper and overlapped papers by turning on Output 1 when one sheet is detected, and turning on Output 2 when two or more sheets are detected.
This means that all the work in applications that would conventionally require two sensors can be done with just a single sensor. - Notable Points
• Minimum detectable height difference of 0.08 mm (BGS-HDL05T)
• AUTO sampling period mode for improved resistance to colors and gloss
• Two individual control outputs
-
- Presence Detection of Glossy and Transparent Pouches
- The BGS-HDL series enables detection of thin food pouches with high gloss.
The FGS mode of the BGS-HDL series ensures stable detection even with transparent pouches, glossy pouches or those with color patterns, and thin pouches. In FGS mode, if the light is reflected from anything other than the background, detection is positive.
Because output is enabled even when laser reception is not possible, stable detection is possible even for highly glossy targets and transparent targets.
- Notable Points
• FGS mode for stable workpiece detection (Sensitivity setting: AUTO configuration or fixed numerical value)
• Minimum detectable height difference of 0.08 mm (BGS-HDL05T)
- Presence Detection of Glossy and Transparent Pouches
-
- High-Accuracy C-MOS Laser Sensors
- BGS-HDL Series
- High-functionality, ultra-high-accuracy height difference sensor
• Minimum detectable height difference of 0.08 mm (BGS-HDL05T)
• Effective against tilted and glossy workpieces
• Two individual control outputs
-